Comprehensive Guide: What is Porosity in Welding and Exactly How to stop It
The Science Behind Porosity: A Comprehensive Guide for Welders and Fabricators
Understanding the elaborate systems behind porosity in welding is vital for welders and fabricators striving for impressive craftsmanship. From the make-up of the base materials to the ins and outs of the welding procedure itself, a wide variety of variables conspire to either aggravate or reduce the presence of porosity.
Comprehending Porosity in Welding
FIRST SENTENCE:
Exam of porosity in welding discloses critical understandings right into the stability and quality of the weld joint. Porosity, identified by the visibility of tooth cavities or voids within the weld steel, is an usual problem in welding procedures. These voids, if not properly dealt with, can compromise the structural integrity and mechanical residential properties of the weld, leading to potential failings in the ended up product.
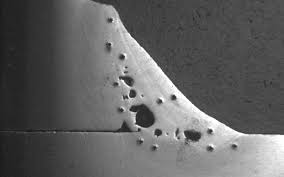
To discover and quantify porosity, non-destructive screening approaches such as ultrasonic screening or X-ray assessment are typically employed. These strategies enable the identification of inner problems without compromising the integrity of the weld. By analyzing the size, shape, and circulation of porosity within a weld, welders can make educated decisions to enhance their welding procedures and accomplish sounder weld joints.

Variables Affecting Porosity Development
The event of porosity in welding is influenced by a myriad of variables, ranging from gas protecting performance to the details of welding specification setups. One crucial variable adding to porosity formation is inadequate gas protecting. When the securing gas, generally argon or carbon dioxide, is not properly covering the weld swimming pool, atmospheric gases like oxygen and nitrogen can contaminate the molten metal, causing porosity. In addition, the sanitation of the base materials plays a considerable role. Impurities such as corrosion, oil, or wetness can vaporize throughout welding, creating gas pockets within the weld. Welding parameters, consisting of voltage, present, travel rate, and electrode type, additionally effect porosity development. Utilizing improper settings can produce extreme spatter or warmth input, which subsequently can cause porosity. The welding method employed, such as gas metal arc welding (GMAW) or protected steel arc welding (SMAW), can affect porosity development due to variations in warm distribution and gas insurance coverage. review Recognizing and regulating these aspects are important for reducing porosity in welding operations.
Impacts of Porosity on Weld High Quality
Porosity development considerably jeopardizes the structural integrity and mechanical residential properties of bonded joints. When porosity exists in a weld, it the original source develops spaces or tooth cavities within the product, minimizing the overall stamina of the joint. These gaps act as stress concentration points, making the weld more at risk to fracturing and failure under lots. The visibility of porosity likewise damages the weld's resistance to rust, as the trapped air or gases within the voids can react with the surrounding environment, leading to deterioration gradually. Furthermore, porosity can impede the weld's capability to withstand stress or effect, additional threatening the general quality and reliability of the welded framework. In crucial applications such as aerospace, automobile, or architectural building and constructions, where safety and durability are extremely important, the damaging results of porosity on weld high quality can have serious repercussions, stressing the significance of decreasing porosity through appropriate welding methods and treatments.
Techniques to Reduce Porosity
Furthermore, using the proper welding parameters, such as the proper voltage, present, and take a trip speed, is critical in avoiding porosity. Keeping a constant arc size webpage and angle during welding likewise helps minimize the chance of porosity.

Utilizing the proper welding method, such as back-stepping or utilizing a weaving movement, can likewise assist distribute heat evenly and reduce the chances of porosity development. By applying these strategies, welders can successfully lessen porosity and create premium welded joints.

Advanced Solutions for Porosity Control
Applying innovative innovations and innovative approaches plays a crucial role in attaining premium control over porosity in welding procedures. One advanced option is the use of advanced gas combinations. Protecting gases like helium or a mixture of argon and hydrogen can aid decrease porosity by providing far better arc stability and boosted gas coverage. In addition, utilizing innovative welding methods such as pulsed MIG welding or changed environment welding can additionally help minimize porosity problems.
An additional advanced service includes the usage of advanced welding equipment. For example, using tools with integrated features like waveform control and advanced source of power can improve weld top quality and lower porosity risks. The application of automated welding systems with exact control over specifications can substantially minimize porosity defects.
Additionally, incorporating advanced monitoring and inspection modern technologies such as real-time X-ray imaging or automated ultrasonic screening can assist in detecting porosity early in the welding procedure, permitting for prompt restorative actions. Overall, incorporating these innovative options can considerably improve porosity control and enhance the total high quality of welded parts.
Final Thought
In verdict, comprehending the scientific research behind porosity in welding is important for welders and makers to produce top notch welds - What is Porosity. Advanced solutions for porosity control can better enhance the welding process and make sure a strong and reputable weld.